22 October 2024
Although hydrogen is emerging as a new energy champion it was actually identified as a distinct element in 1776, and produced without carbon emissions - by splitting water with electricity (electrolysis) – as early as 1800. An internal combustion engine powered by hydrogen and oxygen followed just six years later.
So why has it taken so long to come to the forefront as a clean fuel?
Quite simply, nineteenth-century electrolysis was an expensive, complex process and, with the industrial revolution in full swing, industrialists instead embraced the cheaper, easier process of extracting hydrogen from methane using steam heated up to 1,100°C.
This ‘steam-methane reforming’ (SMR) process spread fast, hand-in-hand with industrial progress, and today still accounts for around 99 % of the 97 million tonnes of hydrogen used by industry annually (of which a third feeds ammonia production for use in sectors as diverse as fertiliser, fabrics, pharmaceuticals and plastics.)
However, this technique has proved costly for the environment. Because methane is sourced from natural gas, coal and oil, every tonne of SMR-produced hydrogen emits greenhouse gases into the atmosphere - as much as 26 tonnes CO2-equivalent (CO2e) in the case of coal.
However, a new combination of engineering innovation and political will is helping to fulfil hydrogen’s original promise not only as a clean and safe fuel, but also a profitable one.
Low/no carbon hydrogen
The focus is on two broad strategies.
1. ’Blue hydrogen’ is still produced through a methane reforming process (either SMR or the more flexible Autothermal Reforming process which employs pure oxygen instead of air). However, the resulting carbon emissions are captured and either re-used in carbon-dependent sectors (so reducing the volume of new fossil fuels processed) or stored safely and permanently deep underground in natural porous rock formations like those associated with depleted oil or gas reserves.
This approach can reduce emissions by up to5 tonne CO2e for every 1 tonne of hydrogen produced – and has the enormous advantage of being deliverable at scale this decade using existing industrial infrastructure and equipment.
2. ’Green hydrogen’ is processed using modern electrolysis techniques powered by renewable energy. While this requires extensive investment in new infrastructure, it has the potential to equalise the emissions-to-production ratio, effectively making the production of hydrogen ‘net zero’.
But to achieve net zero 2050, this requires that emissions be removed from the whole hydrogen lifecycle, including the following stages:
- Compression: Hydrogen gas is either compressed or liquified for easier transportation, or to produce derivatives such as ammonia.
- Transportation: Both hydrogen and its derivatives typically reach their point of use via a pipeline or specialised tankers.
- Storage: The popular options have different advantages. Hydrogen is easily stored as a compressed gas, but this requires high pressure which can increase the risk of leaks, and it has as lower energy density which means it needs more storage space than alternatives. Higher energy density can be achieved through liquefaction (a process that converts hydrogen to liquid state) or solid-state conversion. However, both these processes and their reversal are energy-intensive which compounds technical complexity along the supply chain. Conversion to liquid ammonia requires the additional compression process but retains energy through storage and transportation better than pure hydrogen, and the cleaner versions can use the global storage and transportation network already established for ‘grey ammonia’.
- End use: Hydrogen and its derivatives are typically used for refining petroleum, processing biofuels, treating metals, and producing chemicals and other industrial goods. In liquid form, they’re also excellent carriers and retainers of electrical energy - with enormous potential to support off-grid power plants or to balance demand load.
Engineering cleaner energy
Each of these strategies involves high-intensity processes, increasingly at scale, that are vulnerable to leakage, compromised product integrity or equipment failure.
But since John Crane, a business of Smiths Group, pioneered the first hydrogen gas seal in 1979, engineers have been continuously innovating to overcome evolving challenges. We now have 5,000 critical components securing and enhancing hydrogen projects worldwide, including:
- Mechanical seals that prevent or minimise leaks
- Seal gas recovery systems that optimise resource usage
- Digital monitoring systems that extend seal life and performance
- Couplings that connect parts of rotating machinery securely and manage power transmission flows, and
- Filters that safeguard both product and equipment integrity.
Innovation in action
Together, these have proved to reduce emissions and maintenance costs, improve productivity and accelerate the progress of sustainable industry.
That’s why Canada’s largest blue hydrogen facility relies on our solutions to enhance performance throughout its value chain, from compression to storage and transport. And why the world’s first Gigawatt-scale green hydrogen and ammonia production facility (under construction) is banking on our innovations to help it produce these sustainable products on an unprecedented scale.
It may have taken 250 years. But, as we and others continue to advance the capacity, safety, purity and profitability of the wider hydrogen ecosystem, we’re finally unleashing the true, clean power of this simple but mighty element.
And it’s one that could literally change the world.
Related insights
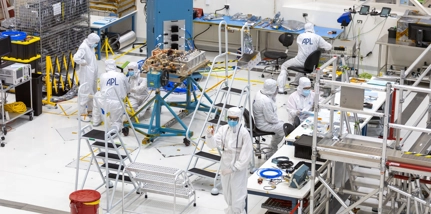
Searching for E.T.
Read our latest Engineering Explained insight on Smiths Interconnect's role in NASA’s Europa Clipper - to search for life on the fourth largest of Jupiter’s 95 moons.
Find out more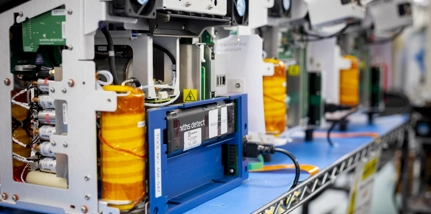
Integrating a sustainable ethos into our products
Find out more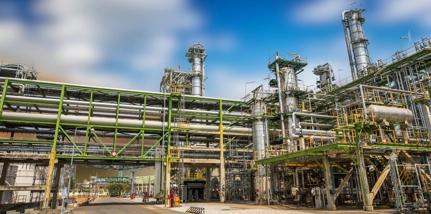