10 November 2023
With its name derived from the Greek word for ‘new’ and the Arabic for ‘future’, Saudi Arabia’s new sustainable regional development - NEOM - promises to ‘change the way we live on this planet.’
Big claims.
And big plans.
Stretching from the Red Sea to Jordan, NEOM’s masterplan covers some 26,500km2 of desert – that’s 4km2 more than the whole of Wales, UK. It features ‘The Line’, a dazzling 110-mile-long, 500m-high, 200m-wide, mirror-walled city for nine million residents; ‘Oxagon’ - a floating industrial city-port dedicated to sustainable innovation and advanced manufacturing; a ski resort; lush parklands; and luxury island destinations.
Billed as a ‘prototype for a better future’, collectively these are intended to showcase ‘an entirely new model for sustainable living.’
As you’d expect, a key pillar of these plans is local renewable electricity generation. But a 4GW wind and solar power farm – whilst mightily impressive – is just the beginning.
The people behind NEOM are thinking much bigger, and much further ahead, by planning the world’s largest green ammonia plant.
Why is that significant?
Ammonia is one of the most common ingredients in a broad array of industrial processes: it is involved in the production of refrigerants, pharmaceuticals, and synthetic fibres as well as mining explosives and, most commonly, in the manufacture of fertiliser that supports some 50% of global food production. Today, it’s mostly made by extracting hydrogen from methane and combining it with nitrogen in a carbon-intensive process that emits up to two tonnes of CO2 for every tonne of usable ammonia created - making the industry one of the dirtiest on the planet. But, with an expanding population of consumers, the global demand for ammonia-dependent products isn’t going to slow down any time soon.
Separately, although renewable power generation is rising rapidly, it has the innate fallibility of weather-dependence and is yet to overcome the enormous challenges of power storage or electric grid capacity and connectivity. So, for now, many global industries – including agriculture and transport - continue to rely on fossil fuels for power rather than electricity or low-carbon alternative fuels.
‘Green ammonia’ can offer a one-stop-solution to these challenges.
Produced through electrolysis with processes powered by electricity generated from renewable sources, green ammonia production is carbon-free. In liquid form, it’s more easily and cheaply bulk-stored than either hydrogen or wind/solar-generated energy and can readily be distributed using existing infrastructure and networks. At its destination, it can then be either ‘cracked’ to release clean hydrogen for fuel, or used whole for electricity generation - which is especially exciting in its potential to support off-grid power plants or to balance demand load.
This flexibility makes it the mass-impact ‘agent of change’ that’s desperately needed if the global Net Zero goal is to be achieved by the critical tipping-point of 2050.
The NEOM Green Hydrogen Company is leading the charge to prove its viability on an industrial scale.
It’s no pipedream. Having secured £6.7 billion of investment, it has begun construction of a plant designed to produce 650 tonnes of green hydrogen per day for domestic use and 1.2 million tonnes of carbon-free ammonia per year for export. Combined, it claims this could save the world of about five million tonnes of carbon per year and help Saudi Arabia to transition its oil-dependent economy.
But – and every game-changer must overcome a big ‘but’ – there are numerous technical challenges to overcome.
One of these is the fact that its weather-dependent renewable energy can’t be generated 24/7. During generation slumps, including every night, the centrifugal compressors must be ‘turned down’ to 60%. This atypical operating pattern for the high-speed, high-torque turbomachinery puts immense stress on their seals: if these become misaligned, they could compromise the integrity and performance of the entire compressor. Or at the very least halt operations until the seals can be repaired or replaced.
Such unplanned stoppages are extremely costly - yet the scale and remote location of NEOM’s compressor field makes physical monitoring 24/7 difficult and prohibitively expensive.
However, with a combination of established and innovative solutions, John Crane has provided the solution.
These include its high-performance H Series couplings which are proven to withstand 2x torque overload and accommodate misalignment safely and reliably.
Plus 20 of its next-generation John Crane Dry Gas Seals for the main process plant centrifugal compressor trains. Drawing on a four-decade heritage, this technology is already proven to extend compressor reliability. And now, thanks to John Crane’s patented diagnostic breakthrough - ‘Sense® Turbo’ - it also answers the remote maintenance question.
Using a unique set of sensors embedded into the seals, Sense will give NEOM’s operators ‘digital eyes’ on the performance and health of the seals. This will enable them to optimise usage and maintenance schedules, nip emerging performance issues in the bud, extend seal longevity and eliminate unplanned downtime.
>>> Tech breakout: Sense Turbo
So: big plans? Yes.
Big claims? Undeniably.
And, with the support of passionate problem-solvers like John Crane, NEOM is now on its way to having a very big impact – as a critical catalyst to delivering emissions targets for aspiring Net Zero economies.

Related insights
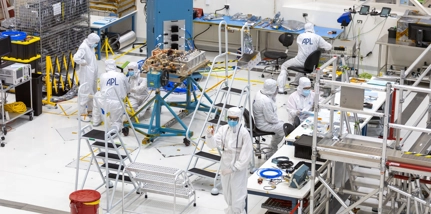
Searching for E.T.
Read our latest Engineering Explained insight on Smiths Interconnect's role in NASA’s Europa Clipper - to search for life on the fourth largest of Jupiter’s 95 moons.
Find out more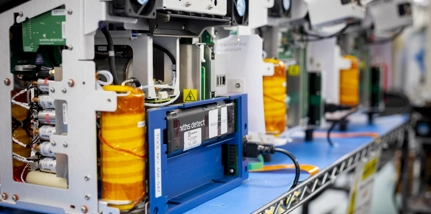
Integrating a sustainable ethos into our products
Find out more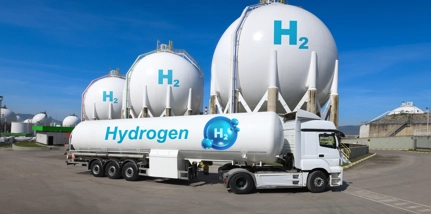
How our engineers are helping hydrogen to become a source of new energy
Read our latest Engineering Explained insight piece on how our engineers are helping hydrogen to become a safe, secure and profitable source of new energy
Find out more