8 May 2024
Engineers have driven all the Ages of the modern era, from the first Industrial Revolution to the Second (Technological), through to today’s Information Age. And now, a series of engineering break-throughs are set to catalyse the next major stage of human history.
Perhaps surprisingly, one of them centres on an age-old material: iron – or, at least, its more common modern form of steel.
Since new processes enabled its mass production from the 1850s, steel swiftly became the backbone not only of many new industries but infrastructure, new ways to transport and travel, and new places in which to work and live. Today, global production is equivalent to the construction of 180,000 Eiffel Towers a year. Such is its prevalence in modern life that its rate of production and application are used as an indicator of a nation’s stage of economic development and ambition.
Over the last 150 years, there have been numerous manufacturing advances to make steel stronger, and easier to produce more quickly, in greater volumes and more cost-efficiently.
But there’s been an enormous cost – to all humans.
The steel industry is still largely powered by fossil fuels, which emit some 3.3 million tonnes of CO2 annually. Along with the emissions and acid wastewater from the mining and shipping of the iron ore used, this makes the industry one of the largest polluters of our planet.
Yet, with the growing acceptance by industrial powers of the imperative to ‘clean up’ steel production, there’s also emerged a strengthening conviction that the sector could, in fact, catalyse another revolution: this time of green industry.
It certainly has the potential to. The more advanced steel production processes have reduced carbon emissions by more than 50% over the last 40 years, and it’s already one of the most recycled materials globally – with up to 60% of all steel products (that’s 1,085 million tonnes) recycled, which avoids the emission of some 950 million tonnes of CO2 that would be generated by new steel production.
What’s more, over 90% of the co-products from the steel making process – such as slag, water, gasses, dusts and energy – are also re-used in the more advanced manufacturing facilities.
And steel is, of course, integral to the world’s transition to clean/renewable energy – providing the essential building material for wind turbines, solar power installations and electric vehicles.
However, there’s still been the very big question of how to produce steel in a carbon-free way. It poses a particularly tough technical challenge because of the extremely high temperatures required to separate the oxygen from the iron ore to deliver the metallic iron at the core for steelmaking. This process - known as the ‘Direct Reduction of Iron (DRI)’ – has traditionally only been possible using natural gas.
But, then, we have some particularly smart engineers in Smiths Group’s Flex-Tek team. In a strategic partnership with Midrex Technologies Inc, the largest producer of reformed iron ore in the world, we took on the problem – and cracked it.
Flex-Tek will supply a large electric heating system powered by renewable energy. By re-designing the DRI reformer to electrically heat hydrogen instead of burning natural gas the system now emits water instead of CO2.
Through 18 months of rigorous testing, our innovations have proved equal to the demands of the operating environment – and recorded CO2 emissions by up to 95% less than the traditional DRI process.
This timely break-through caught the attention of H2 GreenSteel which is the process of constructing the world’s first commercial-scale green steel plant and Europe’s first giga-scale hydrogen electrolyser in Boden (Sweden). With the new Flex-Tek-enabled Midrex H2-DRI system, the plant is on track to ramp up production during 2026.
Together, these pioneers will pave the way for the enormously significant decarbonisation of this ubiquitous industry.
And awaken the dawn of the ‘Age of Green Steel’.
Related insights
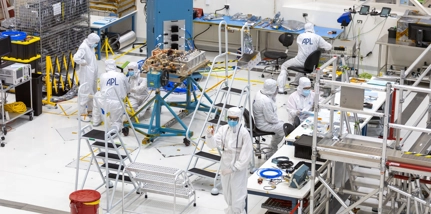
Searching for E.T.
Read our latest Engineering Explained insight on Smiths Interconnect's role in NASA’s Europa Clipper - to search for life on the fourth largest of Jupiter’s 95 moons.
Find out more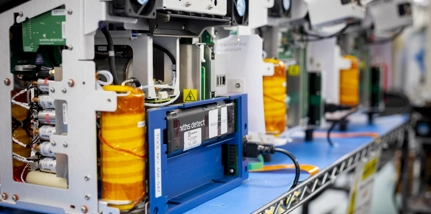
Integrating a sustainable ethos into our products
Find out more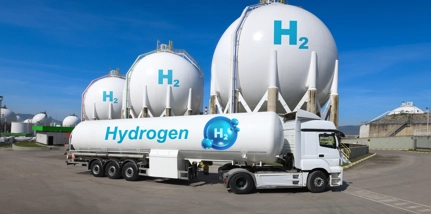
How our engineers are helping hydrogen to become a source of new energy
Read our latest Engineering Explained insight piece on how our engineers are helping hydrogen to become a safe, secure and profitable source of new energy
Find out more