19 June 2024
In the next of our Engineering Explained insight pieces we take a closer look at the mighty mechanical seal, designed and manufactured by our John Crane engineers, and built for high performance in the most challenging of industrial environments.
A brutal operating environment
There’s nothing gentle about the giants of industrial plants today. Compressors and pumps used to increase the pressure and flow of fluids in industrial processes can propel liquid by spinning at up to 50,000 revolutions per minute - that’s more than twice as fast as an F-1 motor; while pressure in gas compressors can build up to a staggering 450 bar(g), some 180 times that inside a standard car tyre.
Some systems must withstand the extreme temperatures that are integral to many chemical processes. Conditions can range from +200°C needed to refine hydrocarbons into gasoline and its byproducts, and as low as -196°C required to liquify gases to improve efficiencies in transportation of fluids.
Others suffer relentless abrasion from substances like mining slurry which is a mixture of liquid with a solids concentration level as high as 40%.
The gap between the dynamic and static components of such systems has always been a point of leakage (emissions), and reduced efficiency and safety. The stresses involved with rotating equipment increase the chance of warping, cracking, and shaft misalignment. The results can be devastating – especially at extreme temperatures or pressures.
The economic impact can also be considerable: halting production at a major Liquefied Natural Gas plant could cost operators up to US$15m a day.
A sealing solution – engineering explained
To combat the issue, engineers historically used a clever product known as ‘gland packing’. This comprised waxed, braided fibres jammed into the gap between the rotating shaft and the equipment’s casing. These packing rings endure constant friction, requiring continuous flushing to cool and regular replacement as they slowly wear down, until the leakage is too large to operate safely and efficiently.
In 1910, John Crane a maintenance engineer from Chicago, upped the game when he plugged a leaky radiator pump with packing rings wrapped with lead foil from tobacco packaging. A succession of patented ‘metallic packing’ products – of which today we still sell nearly enough length each year to reach the moon – rapidly evolved into a century of unrivalled trailblazing in the development of mechanical seals.
Across this period of technological development and industrial advances, the role of mechanical seals has become ever more important. Seals contain the product, keep contaminants out, and minimise downtime by reducing friction, distortion and other damage which can lead to leaks and loss of equipment performance.
But how do they do it?
A highly engineered sandwich
Mechanical seals are constructed a bit like a highly engineered sandwich, with one static face or ‘slice’ fitted to the equipment and one moving face or ‘slice’ fixed to the dynamic rotating shaft. The slices are manufactured to be extremely flat, with one slice being spring-loaded to hold the faces together and to accommodate small deviations of movement.
Between them, the ‘filling’ comprises a fluid which creates a very small gap between the contacting faces, only allowing a small amount of fluid to pass. This reduces the effects of friction, and cools the faces, preventing overheating damage.
Very broadly, today there are two types of mechanical seals: ‘wet’ seals that use a liquid as the buffer fluid and ‘dry’ or gas seals that use gas as the buffer fluid. Wet seals are typically used in equipment processing liquids such as water, crude oil, and paint. Gas seals are typically used in the centrifugal compressors of chemical and petrochemical plants.
Depending on the volatility of the fluid being sealed, and the degree of leak prevention required, these seals are set in single, double, or tandem arrangements (think: club sandwich).
Now, this is where it gets super clever.
An age of innovation
There’s no such thing as ‘one seal fits all.’ Industrial plants today operate in environments ranging from the desert to the poles, handling everything from the minute molecules of hydrogen to the syrupy sludge of wood pulp. Each application needs a seal specific to its circumstances.
For more than a century, our engineers have thrived on such challenges, pioneering patented seal designs to drive the industry forward.
After the world’s first automotive mechanical seal came rotary mechanical seals; then (in the 1980s) we transformed the gas compression industry with non-contacting, gas-lubricated seals that significantly reduced carbon emissions compared to their wet seal predecessors.
Along the way, we’ve innovated edge-welded and formed metal bellows, and spiral grooves to direct liquids or gases in various ways that increase seal longevity while reducing harmful leaks. We’ve developed quick-fit cartridge seals, interchangeable seal platforms, and seals that cope from -200°C to +350°C.
In recent decades, we’ve channelled our engineering expertise into supporting a cleaner industry. Our dry gas seals are designed to reduce methane emissions by up to 95% and extend maintenance intervals by up to 40%. Meanwhile, our diagnostic breakthrough – John Crane Sense® Turbo – gives operators ‘digital eyes’ on their seal performance, using revolutionary sensor technology to help them work smarter, reduce costs and be more efficient.
Industries might have posed some giant problems for our planet, but our team are continuing to make our world safer, cleaner, and more productive - one stride at a time.
Related insights
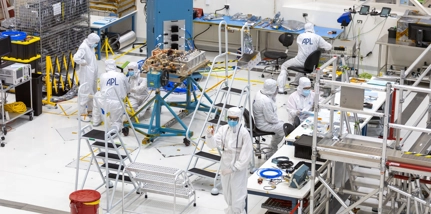
Searching for E.T.
Read our latest Engineering Explained insight on Smiths Interconnect's role in NASA’s Europa Clipper - to search for life on the fourth largest of Jupiter’s 95 moons.
Find out more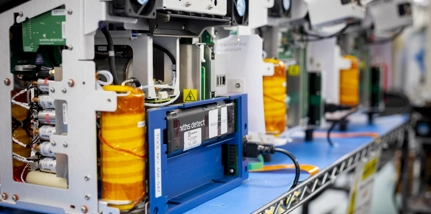
Integrating a sustainable ethos into our products
Find out more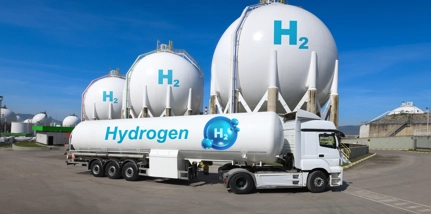
How our engineers are helping hydrogen to become a source of new energy
Read our latest Engineering Explained insight piece on how our engineers are helping hydrogen to become a safe, secure and profitable source of new energy
Find out more