5 July 2020
Today, the work of VentilatorChallengeUK, the Consortium of UK aerospace, motorsport, automotive and medical businesses concludes after more than doubling the stock available to the NHS.
Formed on 19 March in response to the anticipated escalation in COVID19 cases, the Consortium has worked with great determination and energy to deliver critical Penlon ESO 2 and Smiths paraPACTM plus ventilators to the NHS throughout the crisis. In that time, the consortium:
- Scaled-up the Penlon ESO2 Emergency Ventilator device which modified proven clinical equipment, and the Smiths paraPAC PlusTM. Both met clinicians’ requirements as understanding of the virus progressed
- Established, from scratch, seven new large-scale manufacturing facilities at Airbus AMRC Cymru in Broughton, Ford in Dagenham, GKN Aerospace in Luton and Cowes, McLaren in Woking, Rolls-Royce in Filton and STI in Hook, as well as restructuring existing sites Smiths Medical in Luton and Penlon in Abingdon.
- Ventilator peak production exceeded 400 devices a day, with the shortest time taken to achieve 1000 ventilators being 3 days
- Set- up new parallel supply chains and acquired around 42 million parts and electronic components through a complex logistics network that saw DHL design and implement an end-to-end supply chain in only 1.5 weeks
- Despite global competition for parts and lockdown challenges during the pandemic the team sourced part from over 22 countries, with the furthest distance travelled by a single part being 5,226 miles
- Achieved full MHRA approval for the Penlon ESO 2 device in just three weeks, becoming the first newly adapted ventilator design to be given regulatory authorisation as part of the UK Government’s fight against COVID19 and then going on the secure the international quality seal of approval by way of CE marking
- Recruited and trained a 3,500 front-line assembly team in a new age of social distancing, balancing the twin imperatives of speedy delivery with absolute adherence to the regulatory standards needed to ensure patient safety
VentilatorChallengeUK will make its last shipment of finished ventilators on Sunday 5 July after which Consortium businesses will return to regular production.
Dick Elsy, Chairman of VentilatorChallengeUK and CEO of High Value Manufacturing Catapult, said:
“What VentilatorChallengeUK has achieved in the space of twelve weeks is nothing short of incredible, creating and producing an approved product and setting up production facilities on this scale would normally take years. I am immensely proud of the energy, determination and ingenuity shown by every business in responding to this national need.
Together, we have helped ensure the NHS has always had access to the number of ventilators it needs, and we’re pleased to have also contributed to building a resilient stock should ventilators be required in the UK in the future.
This coalition of the very best of this country’s people and capability across different sectors has truly showcased the strength of the manufacturing industry in the UK. While we have now delivered all the required ventilators to the NHS, the Consortium is looking to capture lessons learned and share them across the engineering community – and with Government – as key tools to help UK industry get back on its feet after the COVID19 pandemic has passed.”
Chancellor of the Duchy of Lancaster Michael Gove, said:
“The Ventilator Challenge has been a great success and I would like to thank every manufacturer and designer, and their incredible workforces, for the huge part they’ve played in the national effort to protect our NHS and save lives. In around three months, industry has stepped up to make 14,000 new machines to save lives on the NHS frontline and to help safeguard against any future outbreak.
The Ventilator Challenge has shown that UK manufacturing always rises to the challenge at a time of national need. Everyone involved is truly a hero of the coronavirus crisis.”
Notes to editors:
- For further information on VentilatorChallengeUK and how learnings will be applied to UK industry please refer to: Rosa.Wilkinson@hvm.catapult.org.uk or maeve.harte@outlook.com
For contact with individual businesses please refer to:
Accenture: Andy Rowlands, andy.rowlands@accenture.com
Airbus: Ian Middleton, ian.middleton@airbus.com
AMRC Cymru: James Crossling, j.crossling@amrc.co.uk
Arrow: Thorsten Hecking, thecking@arroweurope.com
DHL: Richard Preece, richard.preece@dhl.com
Ford: John Gardiner, jgardin2@ford.com
GKN Aerospace: Daniel Kendrick, daniel.kendrick@gknaerospace.com
Haas F1: Stuart Morrison smorrison@haasf1team.com
HVM Catapult: Rosa Wilkinson rosa.wilkinson@hvm.catapult.org.uk
Inspiration Healthcare: Brook Nolson, brook.nolson@inspiration-healthcare.com
McLaren: Tim Bampton, tim.bampton@mclaren.com
Mercedes-AMG F1: Bradley Lord blord@mercedesamgf1.com
Meggitt: Diane Whitworth, Diane.Whitworth@meggitt.com
Microsoft: Steve Douthwaite, stevd@microsoft.com
Newton: Juliet Purcell, Juliet.Purcell@newtoneurope.com
Penlon: Craig Thompson, Craig.Thompson@penlon.com
PTC: Jacqui Cook, jcook@ptc.com
Racing Point: Will Hings, will.hings@racingpointf1.com
Renault Sport Racing: Lucy Gennon, Lucy.Genon@uk.renaultsportracing.com
Renishaw: Chris Pockett, Chris.Pockett@Renishaw.com
Rolls-Royce: Emma Fahy, emma.fahy@rolls-royce.com
Siemens UK & Siemens Healthineers: Anne Keogh anne.keogh@siemens.com
Smiths Medical: Andy Collingridge, Andy.Collingridge@smiths.com
STFC Harwell: Amy Pollock, amy.pollock@stfc.ukri.org
STI: Jemma Kirton, Jemma-Kirton@sti-limited.com
Thales: Jackie Lucas, jackie.lucas@uk.thalesgroup.com
Unilever: Helen Fenwick, helen.fenwick@unilever.com
Williams Advanced Engineering: Clare Rose, clare.rose@wae.com
Williams F1: Ann.bradshaw@williamsf1.com
General media enquiries
Contact our global media and communications team at:
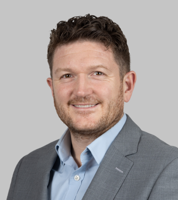
Please note – the press team can only answer enquiries from accredited members of the press.
Related articles
![Davinci Gen V Gen Front View[36]](/media/wlocq5n4/davinci-gen-v-gen-front-view-36.jpg?width=431&height=214&format=webp&quality=100&v=1dbb81c2473de50)
Smiths Interconnect launches ‘DaVinci Gen V’ next-generation test socket
Read our latest company news as Smiths Interconnect launches ‘DaVinci Gen V’ next-generation test socket
Find out more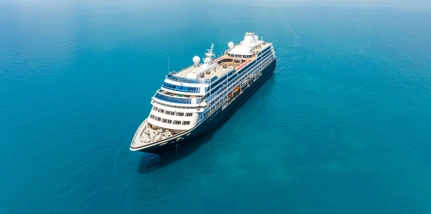
Smiths Detection secures deal to supply systems to major cruise lines
Find out more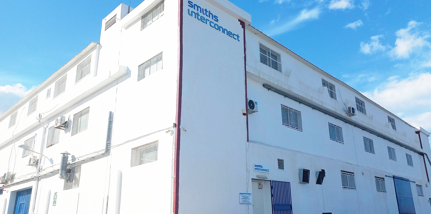
Smiths Interconnect expands EMEA cable harness production capacity
Smiths Interconnect, announces the expansion of its cable harness production capacity at its facility in Tunisia, an investment for growth in support of all its EMEA production sites.
Find out more